LEAN SITE MANAGEMENT (LSM)
Lean Site Management for Life Sciences projects: The parallel activities of different disciplines result in high complexity both of the operational construction site and later of the operation of the building. Lean Site Management (LSM) schedules all building, process and plant planning work exactly using the Lean method. The focus is on a achieving a systematic reduction of buffer and idle times.
HOW IMPORTANT IS LSM TO YOU?
- Do you need to coordinate a range of parallel tasks in different disciplines for your Life Sciences construction project?
- Are unnecessary buffer and idle times repeatedly causing project delays thus triggering additional costs?
- Do you need to find the optimal way to integrate architecture, building services equipment (BSE), and process, laboratory and plant planning?
- Do you need close schedule tracking for your project?
- Do you need an exact overview of progress for individual planners, contractors, suppliers, or your own stakeholders?
HOW WE APPROACH LSM
We develop a takt-time production plan for your construction site in just four simple steps. The overall process analysis forms the basis for process and detailed planning. We use board planning to ensure stable, transparent management of the construction process, and supplement it with our web-based production management platform LCM Digital. This cooperative approach increases productivity and forms the basis for our joint project success.
We lay the groundwork with overall process analysis
Overall process analysis prepares the ground for your construction project. We start by establishing a team comprising construction management, planners, the lean construction manager, and the contracted companies. Together, they work out a ‘recipe’ for the process and define a strategy. In the first step, the construction process is analyzed and broken down into manageable units. The goal is to achieve an optimal cycle time to ensure a smooth process flow with all subprocesses taken into account.
Process planning as the foundation for reliable construction scheduling
It is important to ensure optimal synchronization of the construction process. To achieve this, the entire process is divided into appropriate subprojects and work packages. Resource management for the project is also introduced. This is followed by design of the process with milestones and stability criteria. The logistics concept is developed in parallel to process planning. The LCM experts determine what needs to be done to get the right amount of the right material to the right place at the right time. Demand-driven planning of employees, materials and machines takes place on site, and issues are eliminated in advance.
Board planning as visual work scheduling
The most important visual control tool is board planning using kanban cards. The board shows the construction process for the next four weeks, with precise day-to-day planning. As a simple hands-on tool, board planning encourages all those involved on the construction site to think three to four weeks in advance about how to ensure the construction process runs smoothly. The board shows the individual activities, key data, to-do lists, bottleneck control, and logistics planning, while kanban cards show the current activity for each trade. This also acts as a visual cue as to whether each trade is on schedule.
THE BENEFITS FOR YOU
- Optimized production, commissioning and qualification process right through to shutdown planning for maintenance phases
- Stability of execution
- Transparency of individual services
- Proactivework scheduling
- Reduction of buffer times
- Early detection of disruption
- Well-organized construction site
- Communication between all parties involved
WOULD YOU LIKE TO KNOW MORE ABOUT LEAN SITE MANAGEMENT (LSM)?
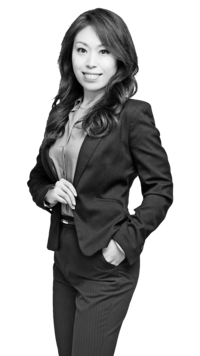